以下是那曲(当地)镀锌管_型材工厂直销的现场实拍视频,让您更好地了解产品的优点和特点不容错过。
以下是:那曲(当地)镀锌管_型材工厂直销的图文介绍

苏沪金属制品有限公司成立于2012年.位于那曲工业园内.是一家专业生产加工、制造的 那曲09CuPCrNi-A钢板、厂家,主要产品有: 那曲09CuPCrNi-A钢板、,公司一贯坚持“质量,用户至上,优质服务,信守合同”的宗旨,凭借着高质量的 那曲09CuPCrNi-A钢板、产品,良好的信誉,优质的服务, 那曲09CuPCrNi-A钢板、产品畅销全国近三十多个省、市、自治区。
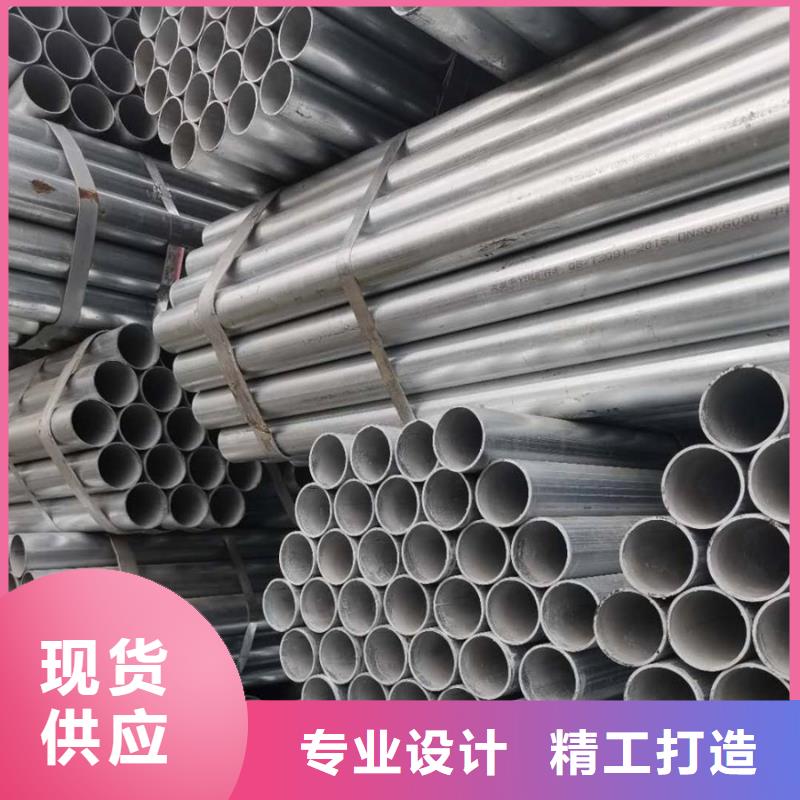

那曲16mn镀锌方管在确保整个制冷过程和无缝钢管的平稳螺旋前进的前提下,可以适当地选择输送滚筒桌的倾斜角度,并可以轻松地控制输送辊桌的倾斜度 . 将热放置在具有特定元素的材料中进行加热和保温,使材料中的特定分子渗透到热表面或产生某些化学物质的土壤层中,改变表面的机理和成分,使零件的表层具有独特的机械或物理性能。接触电阻丝加热热处理:根据电平,对施加5伏以下的工作电压,在电平与的接触点处通过非常大的电流,引起大量电阻发热,使发热表层加热到热处理温度,然后取下电级,将热量传递到发热内部 管子和表面迅速冷却,即达到热处理的目的。 那曲热镀锌管电解加热及热处理:将置于酸、碱或盐溶液的锂电池电解液中,将接负极,接电除尘器阳极氧化。 接通直流电源后,锂电池的电解液被电解,在阳极氧化处放出氧气,在上放出氢气。 氢气将发热的紧紧包围,产生气膜,成为电阻体,引起发热。热表层迅速加热到热处理温度,然后关闭电源,气膜立即消退。锂电池电解液变成淬火物质,使表面迅速冷却硬化。
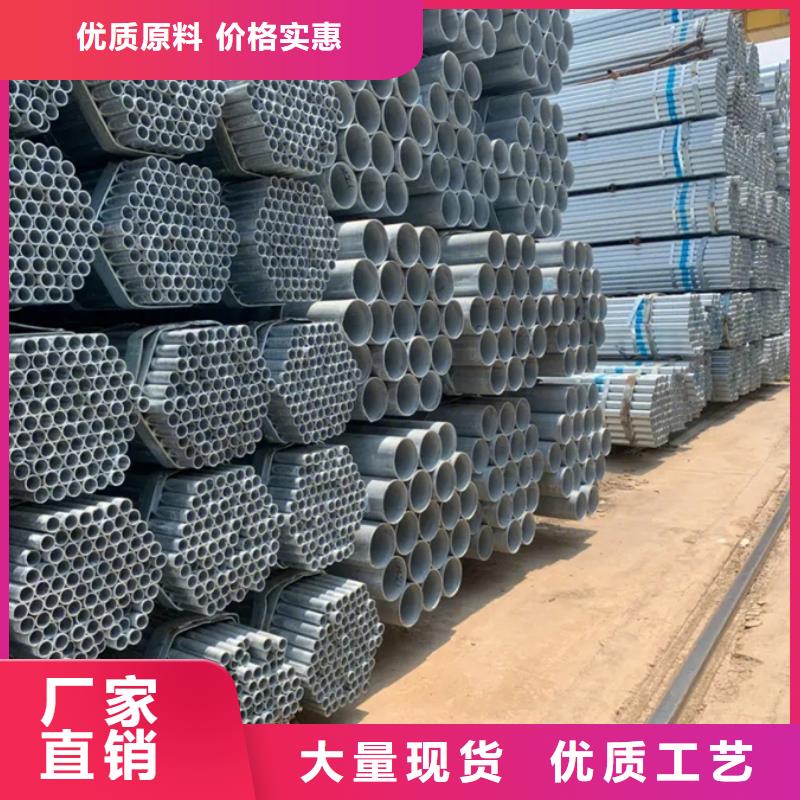

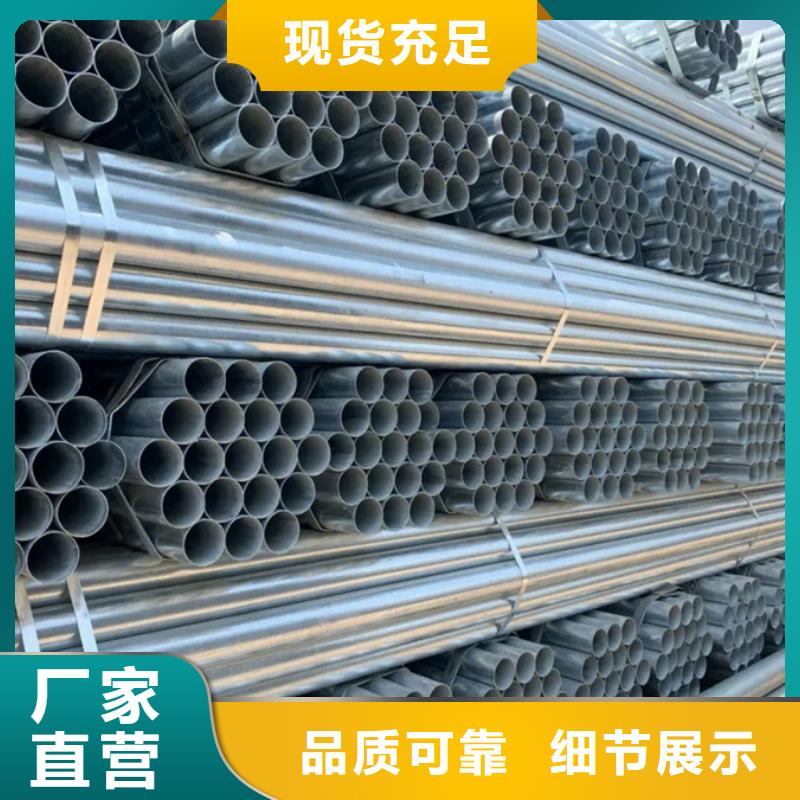
那曲镀锌方管基本上出现在每一个工程项目中。 镀锌方管是一种防腐性能很好的产品,广泛应用于工程建设中的新项目。 镀锌方管的种类很多,或者下面列出了一些常见的类型。 镀锌方管的生产过程中遇到了技术难题。 一般镀锌方管先用液压剪剪,再用复印机剪。 液压剪裁切后,厚钢板一般都有毛刺,造成厚钢板跑偏。 如果正负极偏差超过3mm,需要注意立即调整液压剪板机。 如果客户指定精度高,使用自动或数控机床进行激光切割时孔距困难:镀锌方管的孔一般在中间,仿形机做好90度结构, 准确定位的偏差一般不大。 如果液压剪板机切割不好,会造成孔位偏差较大。 那曲镀锌管在切孔的情况下,复印机应仔细调整开孔模。 一旦设备调整不当,切割孔将不圆。 镀锌方管在很多地方的效果也是不一样的。 很多时候我们要注意质量,因为它的质量比较好,所以在各个领域都有广泛的应用。 关键是因为它的高品质。 强度特别高,在各个领域的作用都比较强,但随着领域的完善和广泛的应用,本产品涉及镀锌方管的特性和质量作为开发,冲压模具的原材料 . 变形、激光切割等生产加工。 因此,对所有无缝管的物理性能都进行了测试。 因此,硬度标准法是如何使用大口径无缝管,物理性能试验方法主要分为两类,一类是拉伸试验,一类是强度试验。


那曲热镀锌管焊接内开口时, 层至第三层必须小规格操作,因为其焊接是影响焊接变形的首要原因。 焊接一到三层后,清洁反面。 应用碳弧气刨去除根部后,需要对焊缝进行机械设备打磨抛光,梳理焊缝表面进行渗氮处理,露出金属织构,防止表面碳化乐观而产生裂纹 . 外口要焊一次,内口会有一些余料。焊接第二层镀锌无缝管时,焊接方向应与 层相反,以此类推。 华尔钢热镀锌钢管每层焊接接头应间隔15-20mm。焊接镀锌无缝管时,两名焊工的焊接电流、焊接速度和焊接叠数应保持一致。 焊接时,焊接应从起弧板开始,在起弧结束板上结束。焊接后切断并打磨和抛光清洁。 焊后热处理:热处理工艺应在焊缝焊好后12小时内进行。 如果不能立即进行热处理工艺,应采用保温、缓冷等方法。 调质处理完毕后,应使用两个热电阻测温,将热电阻焊在焊缝的两侧。
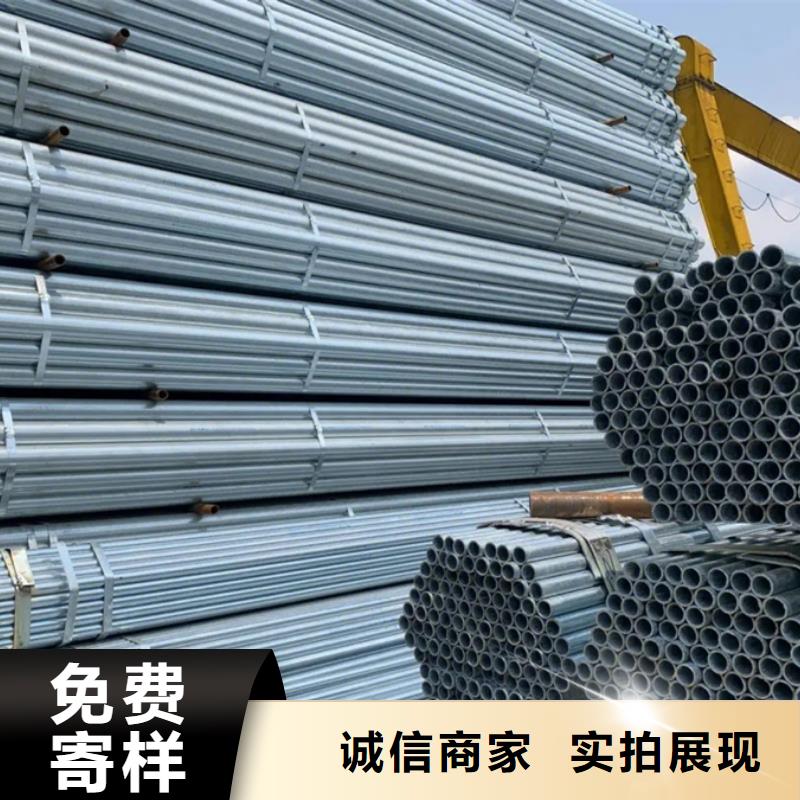